This article looks at some of the common issues that can crop up during the coating process. Here at AFT Fluorotec, we understand how these coating problems occur and how to prevent them.
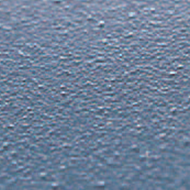
Coating Problem #1: Blistered coatings
Your coating has small blister-like bumps on the coating surface
Probable causes of blistered coatings
- Coating has been applied too thickly.
- Rapid evaporation of solvents (using a solvent that is too volatile), or increasing part temperature too quickly.
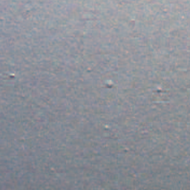
Coating Problem #2: Bubbles or pinholes in coating
Your coating has many small pock marks or tiny holes in the coating.
Probable causes of bubbles or pinholes in coatings
- Excessive agitation which causes coating to foam, trapping gas or air in bubbles.
- Excessive pumping or a leaking pump.
- Rapid evaporation of solvent.
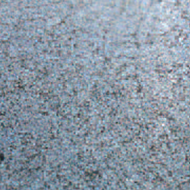
Coating Problem #3: Cobwebbed coatings
Your coating has small strands of coating resin on the surface
Probable causes of cobwebbed coatings
- Fluid coating dries as it is sprayed, before it reaches the surface to be coated.
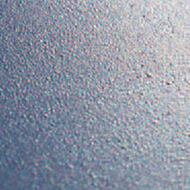
Coating Problem #4: Dry Sprayed coatings
Your coating has a rough, mottled surface, similar to orange peel.
Probable causes of dry sprayed coatings
- The coating is losing too much solvent as it is propelled towards the surface by the spray gun.

Coating Problem #5: Eruptions or pockmarked coatings
Your coating has occasional, random eruptions and/or small pock marks.
Probable causes of eruptions or pock marked coatings
- Microcavities containing air in the metal. The air expands during curing, erupting (outgassing) and leaving either a small eruption or crater.
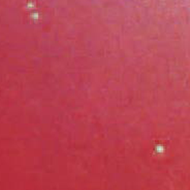
Coating Problem #6: ‘Fish eyes’ in your coatings
Your coating has round crater like holes that penetrate to the substrate
Probable causes of craters in your coatings
- Contaminants that prevent coating from wetting out the surface (such as grease from fingerprints or oil in the compressed air).
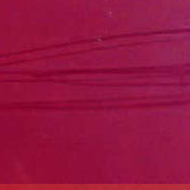
Coating Problem #7: Hazing and dull coatings
Your coating is dull, and has a low reflective appearance.
Probable causes of hazing or dull coatings
- Film of material such as PTFE that rises to the surface (does not harm performance), low temperature / time.
- Presence of moisture (humidity) during coating, leaving a rough, low-gloss surface.
- Over fouling. Low film thickness or rough substrate.
Choosing your coating supplier is a critical decision that can impact the lifetime of your product and the efficiency and profitability of your company.
The whole team within AFT Fluorotec have many years experience within the PTFE and coatings industry and joined AFT with a desire to be part of the next generation of solution providers and innovators within this specialised field.
Get in touch with us to discuss your project and how we can help you out.